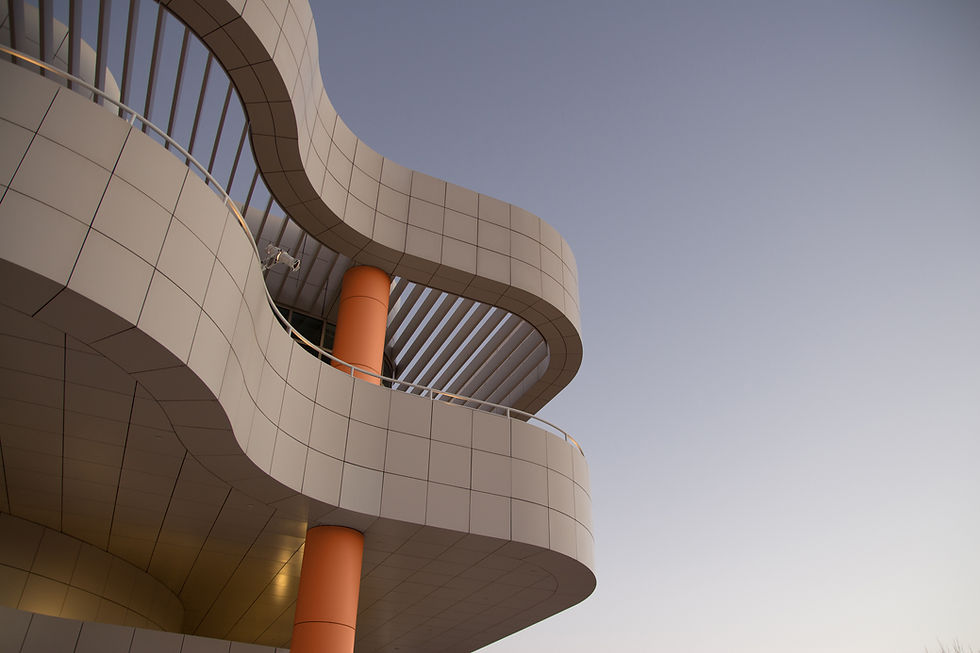
Why the Shipping Industry Is Betting Big on Ammonia
Sep 30
8 min read
2
0
0
Ammonia engines and fuel cells could slash carbon emissions - Maria Gallucci
Illustration: MCKIBILLO
There's a lot to like about ammonia. This colourless feul emits no carbon dioxide when burned. It's abundant and common, and it can be made using renewable electricity, water, and air. Both fuel cells and internal combustion engines can use it. Unlike hydrogen, it doesn't have to be stored in high-pressure tanks or cryogenic dewars. And it has 10 times the energy density of a lithium-ion battery.
For all these reasons, ammonia (NH 3) is gaining favor in the global shipping industry, a multitrillion-dollar machine in need of cleaner fuels to power the freighters and tankers that haul manufactured goods and bulk materials across the ocean. Shipping companies seek climate-friendlier alternatives to petroleum that can propel their behemoth vessels for days or weeks at sea and still leave room on board for cargo.
Maritime shipping contributes nearly 3 percent of annual carbon-dioxide emissions, according to the International Maritime Organization (IMO), the United Nations body that regulates the industry. In 2018, delegates agreed to reduce emissions by 50 percent from 2008 levels by 2050. Meeting that target will require swift and widespread development of diesel-fuel alternatives and new designs for freighters, tankers, and container ships.
Shipowners and industry analysts say they expect ammonia to play a pivotal role in decarbonizing cargo ships. But there's a crucial caveat: No vessels of any size today are equipped to use the fuel. Even if they were, the supply of renewable, or “green," ammonia produced using carbon-neutral methods is virtually nonexistent. Most ammonia is the product of a highly carbon-intensive process and is primarily used to make fertilizers and chemicals.
Recently, though, a handful of projects aim to change that. Finland's Wärtsilä plans to begin testing ammonia in a marine combustion engine in Stord, Norway, by late March. Germany's MAN Energy Solutions and Korean shipbuilder Samsung Heavy Industries are part of an initiative to develop the first ammonia-fueled oil tanker by 2024.
The supply vessel Viking Energy is being retrofitted with a 2-megawatt ammonia fuel-cell system. Ammonia has only half the energy density of traditional fuel, so storing it on board requires much more space. Photo: Eidesvik
Also by 2024, the Viking Energy is poised to become the first vessel propelled by ammonia fuel cells. The Norwegian energy company Equinor (formerly Statoil) charters this offshore supply vessel, which currently runs on liquefied natural gas. Chemical giant Yara will provide the green ammonia, which it plans to produce at a plant in southern Norway.
The initiative “will open up a completely new option for zero-emission shipping," says Henriette Undrum, Equinor's vice president of renewable and low-carbon technology. “We are not just solving one small problem for one ship. It's part of the bigger picture. It will be a starting point to build up the market for zero-carbon fuels."
Still, industry experts say that revamping the global shipping fleet will be extraordinarily expensive. Researchers estimate that up to US $1.4 trillion will be needed to achieve the IMO's emissions-reduction target. And fully eliminating emissions will require an additional $500 billion, according to a January 2020 study by a panel of maritime experts.
A number of climate-friendly technologies are being considered to reach that goal, including fuel cells, hydrogen-storage systems, and large battery packs. Spinning metal cylinders, towing kites, and other propulsion methods are already helping to curb diesel fuel consumption by harnessing the wind. But ammonia will likely dominate among ocean-crossing vessels, which sail for days or weeks between refueling and rely on common infrastructure worldwide. For such ships, “ammonia is the lowest-cost zero-emission fuel that we could find," says Tristan Smith, a researcher at University College London's Energy Institute, which evaluated more than 30 different shipping fuels.
Projected Marine Fuel Use to 2050
As the shipping industry reduces greenhouse-gas emissions, as mandated by the International Maritime Organization, ammonia and hydrogen are projected to be the leading alternatives to traditional oil-based fuels by 2050.
Illustration: Michael Solita. Source: American Bureau of Shipping
Smith predicts green ammonia will be produced in large volumes and will start to be used on ships during the coming decade. Other researchers make similar predictions. According to a September 2019 report from the international consultancy DNV, ammonia could make up 25 percent of the maritime fuel mix by midcentury, with nearly all newly built ships running on ammonia from 2044 onward.
For ammonia-fueled shipping to become a reality, though, several things need to go right. Manufacturers and engineers must overcome key technical hurdles and safety issues in the design of ammonia engines and fuel cells. Port operators and fuel suppliers must build vast “bunkering" infrastructure so ships can fill ammonia tanks wherever they dock. And energy companies and governments will need to invest heavily in solar, wind, and other renewable-energy capacity to produce enough green ammonia for thousands of ships. Globally, ships consume an estimated 300 million tons of marine fuels every year. Given that ammonia's energy density is half that of diesel, ammonia producers would need to provide twice as much liquid ammonia, and ships will need to accommodate larger storage tanks, potentially eating into cargo space.
But if these efforts succeed, it will mark a dramatic revival for a transportation fuel that's largely sat on the sidelines since World War II.
Diesel shortages prompted the first real-world use of ammonia as a fuel. In 1942, German-occupied Belgium was struggling to find enough diesel to run its public buses, just as ridership was increasing. Engineers considered using compressed coal gas, but that fuel's low energy density and awkward storage requirements made it impractical.
Diesel shortages during World War II prompted Belgium to run its public buses on a combination of ammonia and coal gas. Photos: Energy Institute
In April 1943, Ammonia Casale (now part of the Swiss fertilizer maker Casale) introduced an internal combustion engine that could run on a blend of ammonia and coal gas. Some 100 buses in Belgium adopted the system, dubbed Gazamo. But the bus operator returned to using diesel once supplies reappeared.
Over the ensuing decades, research on ammonia engines has come in fits and starts, even as ammonia supplies soared. In the 1930s, worldwide annual production of ammonia was about 300,000 metric tons. Today, the world produces about 150 million metric tons of ammonia every year. While ammonia is valuable as a chemical feedstock, the transportation sector has had little incentive to use it. Petroleum has a higher energy density and is easier and cheaper to produce.
“Now, with a focus on having carbon-neutral fuels, it's obviously a different discussion. The economics around it are very different," says Peter Kirkeby of MAN Energy Solutions. “Everybody wants to know, 'When can we have the ammonia engine?' "
Kirkeby spoke from Copenhagen, where the company has a large waterfront facility on the city's south harbor. MAN, a subsidiary of Volkswagen, develops multimegawatt diesel engines for ships and power generators. The Danish outpost has designed marine engines that run on methanol, liquefied natural gas, liquid petroleum gas, and other alternative fuels. Kirkeby says the industry's recent push for ammonia comes as renewable-energy producers are seeking new markets, and as shipping companies look for emission-cutting solutions.
How To Produce “Green" Ammonia
The traditional Haber-Bosch process is used to produce virtually all of the world's ammonia, but it is energy and carbon intensive. To decarbonize the ammonia-making process, electricity from renewable sources, such as wind and solar power, is used to electrolyze water, yielding hydrogen (as well as oxygen). The electricity is also used to separate air, yielding nitrogen (as well as oxygen and some argon and carbon dioxide). The hydrogen is then reacted with the nitrogen to produce ammonia, NH 3. Cargo ships equipped with ammonia-burning internal combustion engines or ammonia fuel cells are expected to help the shipping industry halve its carbon-dioxide emissions by midcentury . Illustration: MCKIBILLO; Source: MAN Energy Solutions
Ammonia is a simple molecule, composed of three hydrogen atoms bonded to a single nitrogen atom. Today, most industrial hydrogen is produced using an energy-intensive method called steam methane reforming, which causes the methane in natural gas to react with steam and releases hydrogen, carbon monoxide, and a small amount of carbon dioxide. Nitrogen is mainly produced by cooling air to separate it into its constituent gases: nitrogen, oxygen, argon, and carbon dioxide.
To make ammonia, hydrogen and nitrogen are reacted with a catalyst at high temperature (about 500 °C) and high pressure (20 to 40 megapascals) via an industrial process developed by the German chemists Fritz Haber and Carl Bosch more than a century ago. To be stored in large quantities, ammonia can be liquefied by putting it under pressure (about 1 MPa at 25 °C) or refrigerating it (to –33 °C). All told, the Haber-Bosch process accounts for 1.8 percent, or half a billion metric tons, of human-caused global CO2 emissions each year.
If ammonia is to play a part in reducing maritime emissions, the fuel must be made in a cleaner way. For example, the hydrogen can be made through electrolysis, splitting water into hydrogen and oxygen using electricity from a renewable source such as wind or solar power. Renewable energy can also be used to separate nitrogen from air.
A trial plant at the Fukushima Renewable Energy Institute in Japan [top] uses solar power to produce up to 50 kilograms of green ammonia a day. A demonstration system [bottom] at the Rutherford Appleton Laboratory in England is powered by a wind turbine and makes up to 30 kg of green ammonia daily. Photos, top: JGC Holdings Corp.; bottom: Science and Technology Facilities Council, UK
Boosting fuel supplies and building fuel-distribution infrastructure are the biggest challenges to ammonia-powered shipping, experts say. Only tiny amounts of green ammonia are now being produced. A trial plant at the Fukushima Renewable Energy Institute in Japan uses solar power and water electrolysis to produce 20 to 50 kilograms of green ammonia per day. A demonstration system at the Rutherford Appleton Laboratory, in Oxfordshire, England, is powered by an on-site wind turbine and makes up to 30 kg of green ammonia daily. [For a look at how a farmer in Iowa is using solar power to produce green ammonia, see "A Retired JPL Engineer's Journey: From Space Probes to Carbon-Neutral Farming."]
Larger initiatives are underway in Australia, Chile, and New Zealand. In Queensland, for example, the Australian Renewable Energy Agency recently backed a A$3.9 million (US $3.0 million) feasibility project for a plant that could produce 20,000 metric tons of ammonia annually, using 208 gigawatt-hours of electricity. The global shipping industry used the equivalent of 3.05 million GWh in 2015. Substituting just 10 percent of that total with green ammonia will require some 550,000 GWh of renewable electricity, according to the Korean Register of Shipping.
As green ammonia slowly scales up, the shipping industry will have to solve some other problems. The top concern is ammonia's toxicity. In concentrated form, the pungent, colorless gas can be deadly. In January 2020, a spill of nearly 3,000 liters of liquefied ammonia fertilizer in Illinois sent more than 80 people to the hospital with chest pain, eye irritation, cough, and severe headache. Ammonia manufacturers and distributors must follow strict handling and safety guidelines to minimize the potential for disaster. To use ammonia fuel, ships will need additional safety equipment, such as emergency ventilation and gas-absorption systems.
Fortunately, operators of chemical tankers—large vessels designed to transport hazardous products—already have experience handling ammonia. About 10 percent of annual production is transported by sea. These ammonia tankers may be among the first vessels to use the chemical for fuel, in the same way that today's liquefied natural gas carriers burn some of their own cargo while sailing.
Still, using ammonia in the engine room poses new risks. MAN's engine will likely include double-walled fuel pipes to prevent gas from escaping should the inner pipe leak or rupture. A mechanical ventilation system will intercept any leaking gas and alert the ship's crew.
The Shipping News
This article appears in the March 2021 print issue as “The Ammonia Solution."